Boosting Business with 3D Selective Laser Sintering
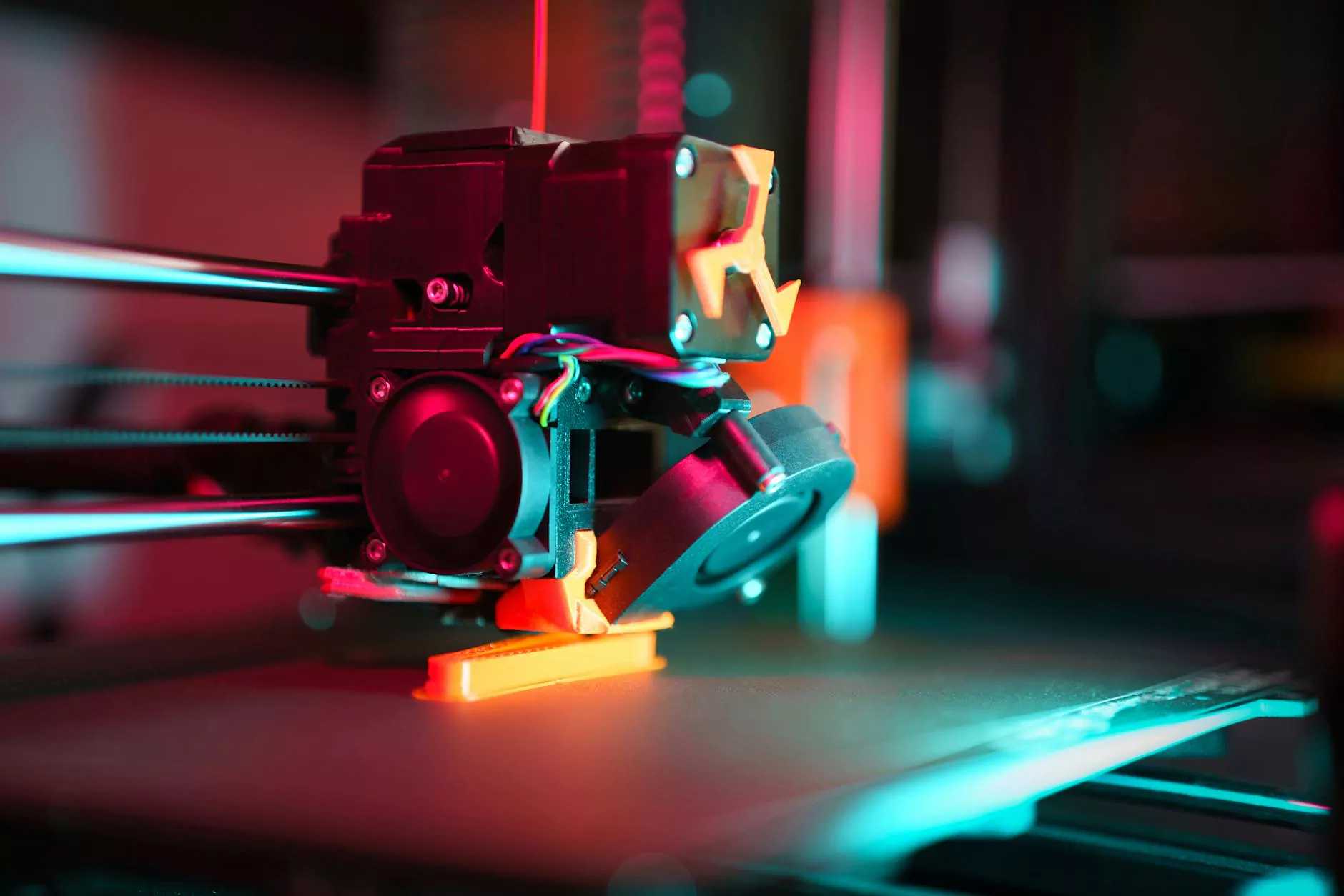
In today's competitive business landscape, staying at the forefront of technological advancements is crucial for sustainable growth and success. One such breakthrough that has revolutionized the Metal Fabricators and 3D Printing industries is 3D Selective Laser Sintering (SLS). Quick Parts, a leading provider in the field, has embraced this cutting-edge technology to offer unmatched solutions to businesses seeking to innovate, enhance productivity, and streamline their manufacturing processes.
Understanding 3D Selective Laser Sintering
3D Selective Laser Sintering (SLS) is an additive manufacturing process that utilizes powdered materials, often metal alloys, to create highly intricate and durable components. This technique involves layering the material using a high-powered laser that selectively sinters the powdered particles, fusing them together to form solid structures.
The integration of 3D SLS technology at Quick Parts has opened up a multitude of opportunities for businesses seeking enhanced flexibility, precision, and efficiency in their manufacturing processes. By harnessing this innovative approach, Quick Parts ensures the production of complex geometries that would be otherwise challenging or impossible to achieve with traditional methods.
The Benefits of 3D Selective Laser Sintering
By employing 3D Selective Laser Sintering, Quick Parts offers a wide range of benefits to businesses across various industries:
1. Design Freedom and Complexity
3D SLS breaks free from the constraints of traditional manufacturing methods, allowing businesses to unleash their creativity and explore innovative design concepts. Complex, organic shapes that were previously difficult to produce can now be effortlessly realized with the precision and accuracy offered by this technology.
2. Rapid Prototyping and Iteration
With 3D SLS, businesses can expedite the prototyping phase, reducing time-to-market and gaining a competitive edge. Quick Parts' expertise in this field enables quick iterations, facilitating design improvements, product testing, and refinement, all facilitated by the speed and efficiency of the SLS process.
3. Cost-Effective Small Batch Manufacturing
The digital nature of 3D SLS eliminates the need for costly tooling and molds traditionally associated with small batch manufacturing. This allows businesses to produce low volumes of highly customized components without incurring exorbitant setup costs, making it an ideal solution for niche markets or personalized products.
4. Superior Strength and Durability
3D Selective Laser Sintering produces components with exceptional mechanical properties, making them suitable for demanding applications that require high strength and durability. The precise fusion of particles creates structures that exhibit excellent thermal, chemical, and mechanical resistance, outperforming components produced through conventional methods.
Applications of 3D Selective Laser Sintering
The versatility of 3D SLS technology extends to a myriad of industries, where Quick Parts expertly caters to their specific needs:
1. Aerospace and Defense
In the aerospace and defense sectors, where lightweight yet robust components are critical, 3D Selective Laser Sintering emerges as a game-changer. The ability to create intricate parts with reduced weight and high structural integrity makes it an attractive additive manufacturing option for aircraft, unmanned systems, and defense equipment.
2. Medical and Dental
With its ability to comply with stringent medical standards, 3D SLS has become an indispensable tool in the production of surgical guides, orthopedic implants, and dental prosthetics. Quick Parts' expertise in this sector ensures the delivery of precise, biocompatible components that meet the demanding requirements of medical professionals.
3. Automotive and Motorsports
The automotive and motorsports industries heavily rely on 3D Selective Laser Sintering to manufacture lightweight components that enhance performance, reduce fuel consumption, and improve aerodynamics. Quick Parts' advanced SLS capabilities empower businesses to stay ahead of the curve by producing complex parts and prototypes with exceptional strength-to-weight ratios.
4. Industrial Manufacturing
In the realm of industrial manufacturing, the integration of 3D SLS technology offers opportunities for enhanced customization and accelerated production. It allows businesses to produce intricate jigs, fixtures, and tooling, improving efficiency and reducing downtime associated with traditional manufacturing methods.
Quick Parts: Your Partner in Innovation
Quick Parts, with its forward-thinking approach and commitment to excellence, serves as a pioneer in the field of 3D Selective Laser Sintering. By diligently incorporating this technology into their processes, they empower businesses with unparalleled manufacturing solutions, opening doors to endless possibilities.
With a team of skilled engineers and technicians, Quick Parts ensures that each project receives personalized attention and expertise. Their comprehensive knowledge and experience in 3D SLS guarantee the precise realization of intricate designs, outstanding mechanical properties, and superior product performance.
Partnering with Quick Parts means gaining access to cutting-edge technology, customized solutions, and the ability to stay ahead of the competition in today's fast-paced business environment. The integration of 3D Selective Laser Sintering is a leap toward increased innovation, efficiency, and profitability.
Discover the transformative power of 3D SLS today and unlock a world of possibilities for your business with Quick Parts, the industry leader in Metal Fabricators and 3D Printing. Reach out to Quick Parts to discuss your project requirements and learn more about their extensive range of services.