Understanding Plastic Injection Moulding: The Key to Efficient Manufacturing
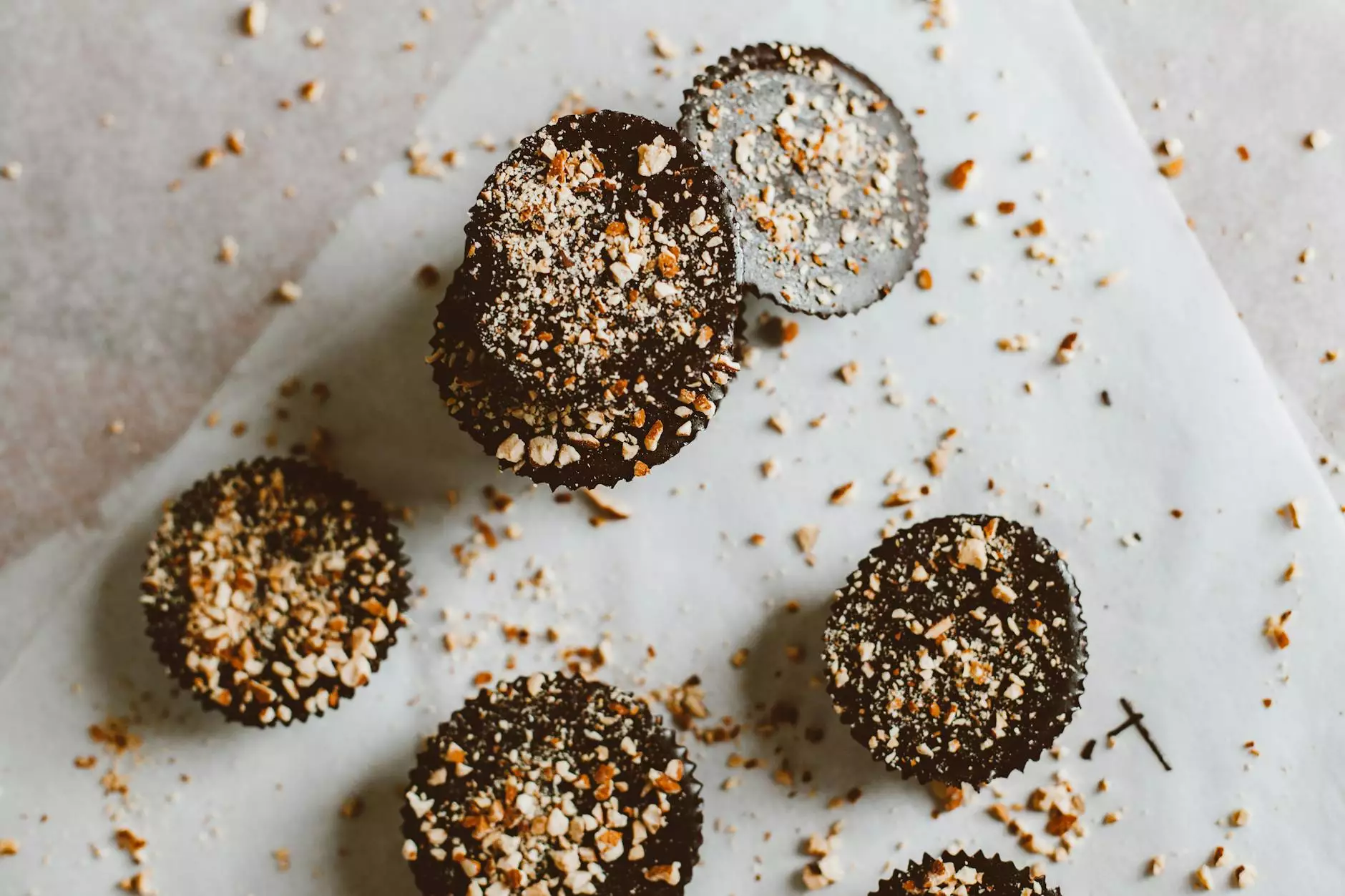
Plastic injection moulding is an advanced manufacturing process that plays a pivotal role in today’s industrial landscape. This technique allows businesses, particularly metal fabricators, to produce high-quality plastic components with remarkable precision and efficiency. In this comprehensive article, we will explore the intricacies of plastic injection moulding, its benefits, applications, and its significant impact on various industries, including insights relevant to Deep Mould.
What is Plastic Injection Moulding?
Plastic injection moulding is a manufacturing process where molten plastic is injected into a mould to create specific shapes and designs. This method is highly sought after in the production of intricate parts that require tight tolerances and high repeatability. The process involves several key steps:
- Material Selection: Choosing the right type of plastic for the intended application.
- Heating: The selected plastic granules are heated until they become molten.
- Injection: The molten plastic is injected into the mould under high pressure.
- Cooling: The material is allowed to cool, solidifying into the desired shape.
- Demoulding: The hardened part is removed from the mould.
Benefits of Plastic Injection Moulding
The popularity of plastic injection moulding can be attributed to several notable advantages:
1. High Efficiency and Speed
One of the most significant benefits of plastic injection moulding is its speed. Once the mould is created, it can produce thousands of parts in a short period, drastically reducing production time. This efficiency is vital for businesses aiming for high-volume production.
2. Design Flexibility
Plastic injection moulding allows for a wide range of intricate and complex designs that can be tailored to meet specific client needs. The versatility of designs maximizes creativity while ensuring functionality.
3. Cost-Effectiveness
Although the initial cost of developing injection moulds can be high, the long-term savings are undeniable. The high-speed production and minimal waste generated during the process significantly lower the cost per unit, making it economical for large-scale manufacturing.
4. Excellent Surface Finish
Parts produced through injection moulding often have a superior surface finish, reducing the need for additional processing and thereby saving time and costs.
5. Strong and Durable Products
The resulting products from this process are typically strong, tough, and resistant to various environmental conditions, making them suitable for a wide range of applications.
Applications of Plastic Injection Moulding
The applications of plastic injection moulding span various industries due to its versatility. Here are some key sectors that benefit from this technology:
1. Automotive Industry
The automotive sector utilizes plastic injection moulding to produce countless components such as dashboards, bumpers, and interior parts. This method enables the production of lightweight yet durable parts that are crucial for vehicle efficiency.
2. Consumer Goods
Everyday items such as toys, kitchenware, and packaging are often created through plastic injection moulding. The ability to produce high volumes quickly allows manufacturers to meet consumer demands effectively.
3. Medical Devices
In the medical field, precision is paramount. Plastic injection moulding produces components for various devices, ensuring they meet strict regulatory standards while maintaining quality and safety.
4. Electronics
From housings to internal components, the electronics industry utilizes plastic injection moulding to create parts that are lightweight, complex, and cost-effective.
5. Industrial Components
Many machinery and equipment parts are manufactured through this process, allowing for tailored solutions that meet specific operational requirements.
How Plastic Injection Moulding Works: A Step-by-Step Guide
To fully appreciate the intricacies of plastic injection moulding, it's essential to understand the detailed workings of the process. Below is a breakdown of each step:
1. Material Preparation
Granular plastic materials are fed into a hopper. Depending on the application, different types of polymers may be used, selected for their unique properties (e.g., ABS, PVC, Polyethylene).
2. Heating and Melting
The plastic granules are then transferred into a heated barrel, where they are melted using a combination of heat and mechanical force from a reciprocating screw. This phase includes careful temperature control to ensure proper melting without degrading the material.
3. Injection into the Mould
Once the plastic is molten, it is injected into a pre-designed mould. The injection occurs under high pressure to ensure that the material fully fills all cavities of the mould, capturing every detail of the design.
4. Cooling and Solidification
After injection, the molten plastic cools and solidifies inside the mould. This cooling phase is critical for maintaining the shape and properties of the final product.
5. Ejection
Once the component has cooled sufficiently, it is ejected from the mould using ejector pins. This action must be carefully controlled to prevent damage to the finished part.
Challenges and Considerations in Plastic Injection Moulding
While plastic injection moulding is a highly efficient process, it comes with its own set of challenges:
1. Initial Setup Costs
The costs associated with designing and producing a mould can be significant, especially for low-volume production runs.
2. Mould Maintenance
To ensure consistent quality, moulds require regular maintenance and may need repairs over time, which can add to operational costs.
3. Material Limitations
Not all plastics are suitable for injection moulding. It is essential to carefully choose the right type of plastic based on the application.
Why Choose Deep Mould for Your Plastic Injection Moulding Needs
When it comes to choosing a reliable partner for plastic injection moulding, Deep Mould stands out as a leader in the field. Here are some reasons why:
1. Expertise and Experience
With years of expertise in plastic injection moulding, Deep Mould has a robust understanding of various materials and processes, ensuring high-quality outcomes for all projects.
2. Advanced Technology
Utilizing state-of-the-art machinery and techniques, Deep Mould ensures precision and efficiency in every aspect of production. This investment in technology translates to superior products and quicker turnaround times.
3. Customized Solutions
Deep Mould offers tailored solutions that meet the unique needs of clients across various sectors, delivering products that align with specific requirements and standards.
4. Quality Assurance
Strict quality control measures are in place to ensure that every product produced meets the highest standards of performance and safety.
5. Sustainable Practices
Deep Mould is committed to sustainability, employing practices that minimize waste and reduce environmental impact while producing high-quality components.
Conclusion
In conclusion, plastic injection moulding is an indispensable process in modern manufacturing, providing efficiency, design flexibility, and cost-effectiveness that drive numerous industries. Understanding its workings and advantages is essential for businesses looking to optimize their production capabilities.
At Deep Mould, we pride ourselves on being at the forefront of this technology, offering innovative solutions tailored to our clients' specific needs. By choosing the right partner in plastic injection moulding, businesses can enhance their manufacturing processes and achieve remarkable success.